Struggling with determining the right warehouse storage space for your commercial moving needs? It's a common challenge, and we're here to help simplify it. Our guide introduces the use of a warehouse storage cost calculator, an essential tool for balancing space and budget effectively.
RCS Moving & Storage brings expertise in commercial relocation to your fingertips. This guide is infused with our knowledge, showing you how to use a warehouse storage cost calculator to optimize space and minimize costs efficiently.
Dive into this guide for insights on optimizing warehouse space, reducing costs, and improving business efficiency. Whether you're experienced or new to commercial moving, you'll find practical strategies and tools here to enhance your warehouse management.
Understanding Warehouse Storage Costs
Cost efficiency in warehousing is not just a goal; it's a necessity for business success. Understanding and managing warehouse storage costs effectively is the linchpin for achieving significant savings and operational excellence. This process starts with identifying the key components that contribute to overall storage costs.
At the heart of effective warehouse management lies accurate inventory data entry. It is more than just a routine task; it's the foundation that supports efficient stock level tracking, leading to enhanced space utilization and streamlined cost management. Proper inventory management ensures that every square foot of warehouse space is used to its maximum potential, reducing wasted space and associated costs.
Maximizing Efficiency with the Right Racking System
Choosing the right racking system is a crucial decision that greatly influences your warehouse's efficiency and cost-effectiveness. The appropriate system not only optimizes storage density and selectivity but also plays a significant role in the overall functionality of your storage space.
Understanding the diverse types of racking systems and their unique benefits can lead to a more organized, space-efficient, and cost-effective warehouse operation.
{GRAPHIC}
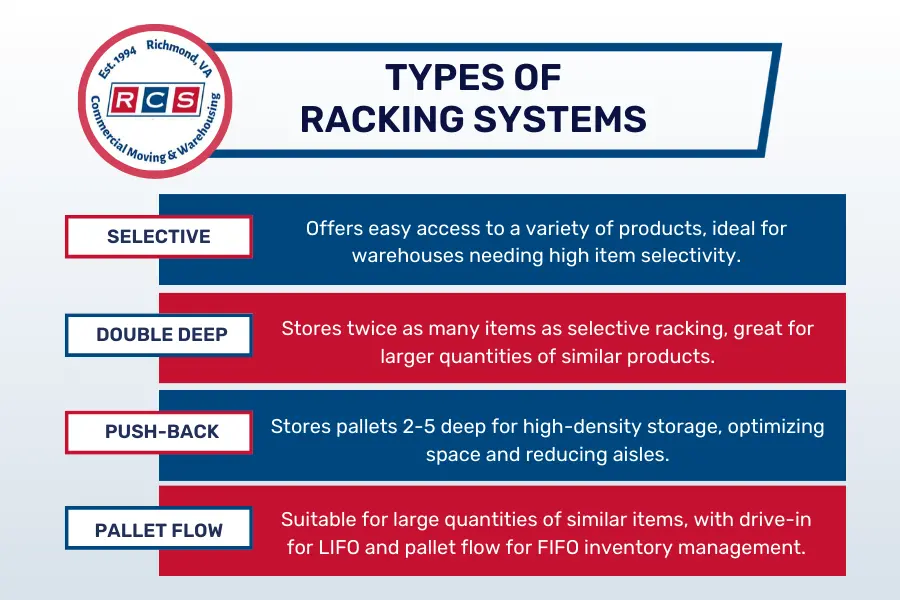
- Selective Racking: Ideal for warehouses requiring high selectivity, these systems offer easy access to all items, making them perfect for a wide variety of products.
- Double Deep Racking: This system doubles the storage capacity compared to selective racking, suitable for larger quantities of fewer product types.
- Push-Back Racking: Designed for high-density storage, it allows pallets to be stored 2-5 deep while offering easy access, optimizing space and reducing aisle count.
- Drive-In and Pallet Flow Systems: These are excellent for storing large quantities of similar products. Drive-in systems are ideal for 'last in, first out' (LIFO), while pallet flow systems suit 'first in, first out' (FIFO) inventory management.
Strategizing Warehouse Space for Optimal Efficiency
Effective utilization of warehouse space is a critical aspect that goes beyond mere organization – it's a strategic business decision. By optimizing warehouse layout and understanding the dimensions of pallets and products, businesses can significantly enhance their storage efficiency. This strategic approach involves not just arranging space, but also understanding and utilizing every inch for maximum benefit.
- Effective Storage Configuration: Through careful planning and layout design, optimizing warehouse space usage becomes achievable, leading to improved cost-efficiency and operational flow.
- Understanding Pallet and Product Dimensions: Knowing the exact dimensions of pallets and products is essential for efficient space allocation and can dramatically impact the overall storage capacity and handling efficiency.
- Maximizing Space with Smart Design: Incorporating smart design principles in warehouse layout planning can result in more efficient use of space, reducing waste and increasing productivity.
- Dynamic Space Management: Adapting the warehouse layout to fit changing inventory needs ensures that space is always used in the most efficient way possible.
Enhancing Efficiency through Cubic Utilization in Warehouses
Making the most of every cubic foot in your warehouse is a critical strategy for enhancing efficiency and reducing costs. Achieving optimal cubic utilization is about more than just filling space; it's about intelligent design that considers both vertical and horizontal dimensions. This approach not only increases storage capacity but also plays a significant role in reducing overhead costs and improving overall warehouse functionality.
- Optimizing Space Vertically and Horizontally: By maximizing storage space in both dimensions, you can significantly enhance space efficiency, accommodating more inventory within the same footprint.
- Aisle Width and Accessibility: Careful planning of aisle widths and accessibility is essential for ensuring smooth operational flow and safety. This consideration impacts not just space usage but also the productivity and safety of staff and machinery.
- Strategic Design for Maximum Utilization: Implementing a strategic design that optimizes every aspect of warehouse space can lead to substantial savings and improved operational efficiency.
- Balancing Storage and Accessibility: It's crucial to strike the right balance between maximizing storage space and maintaining easy accessibility for efficient warehouse operations.
Prioritizing Safety and Efficiency in Warehouse Operations
The harmony between safety and efficiency is not just important, it's essential for success. A well-managed warehouse ensures safe operations while also maintaining high inventory turnover and easy accessibility. This balance is key to creating a productive and secure workplace, where safety protocols complement operational efficiency.
{GRAPHIC}
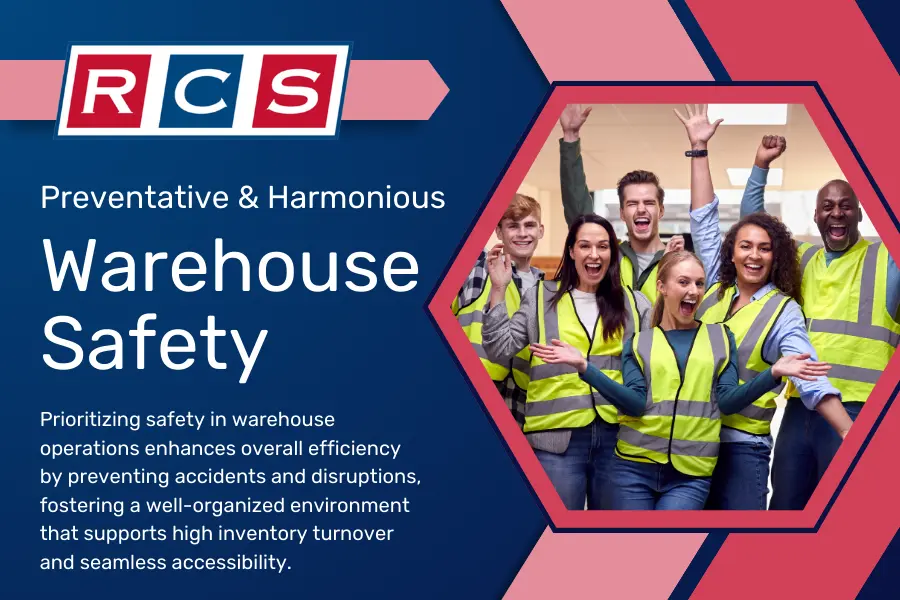
- Ensuring a Secure Workspace: Implementing and maintaining adequate safety margins is crucial to prevent accidents and disruptions. This involves setting and adhering to safe distances and limits within the warehouse, ensuring a safe environment for staff and machinery.
- Inventory Turnover and Accessibility: Achieving a balance between high inventory turnover and accessibility is vital for optimal warehouse operations. This balance ensures a steady and efficient flow of goods, while also facilitating easy access for handling and transport.
- Creating a Safety-First Culture: Fostering a safety-first culture within the warehouse not only enhances employee well-being but also contributes to overall efficiency and productivity.
- Efficiency Without Compromising Safety: Striving for operational efficiency should never come at the cost of safety. Effective warehouse management finds the middle ground where both can coexist and support each other.
- Regular Safety Training and Audits: Conducting regular safety training and audits is key to maintaining a safe warehouse environment. This proactive approach ensures that all staff are aware of safety protocols and that the warehouse adheres to the latest safety standards.
- Technological Integration for Safety Monitoring: Utilizing technology for safety monitoring, such as surveillance systems and automated alerts, can significantly enhance the safety of warehouse operations. This integration helps in early detection of potential hazards and quick response to emergencies.
Adapting to Seasonal Variations in Warehouse Management
Seasonal fluctuations present unique challenges in warehouse management, significantly impacting storage requirements. To maintain efficiency and control costs, it's crucial to adapt your storage strategies to these changes. This adaptation not only ensures a smooth operational flow throughout different seasons but also helps in optimizing storage costs and space utilization.
- Recognizing Seasonal Impact on Storage: Being aware of how different seasons affect your inventory levels is key to proactive warehouse management.
- Flexible Storage Strategies: Developing flexible storage strategies allows for adjustments in space allocation to accommodate seasonal inventory fluctuations, ensuring efficient use of warehouse space year-round.
- Cost-Effective Management of Seasonal Inventory: Adapting storage strategies for seasonal changes can lead to more cost-effective warehouse operations, preventing unnecessary expenditure on unused space.
- Efficient Utilization of Resources: By anticipating and planning for seasonal variations, warehouses can make better use of their resources, including space, staff, and equipment.
Conducting Comprehensive Cost Analysis in Warehouse Operations
A thorough cost analysis is fundamental to the financial health of any warehouse operation. It involves a detailed examination and understanding of all expenses associated with running a storage facility. This process is critical not only for identifying cost-saving opportunities but also for ensuring the overall profitability and sustainability of the operation.
{GRAPHIC}
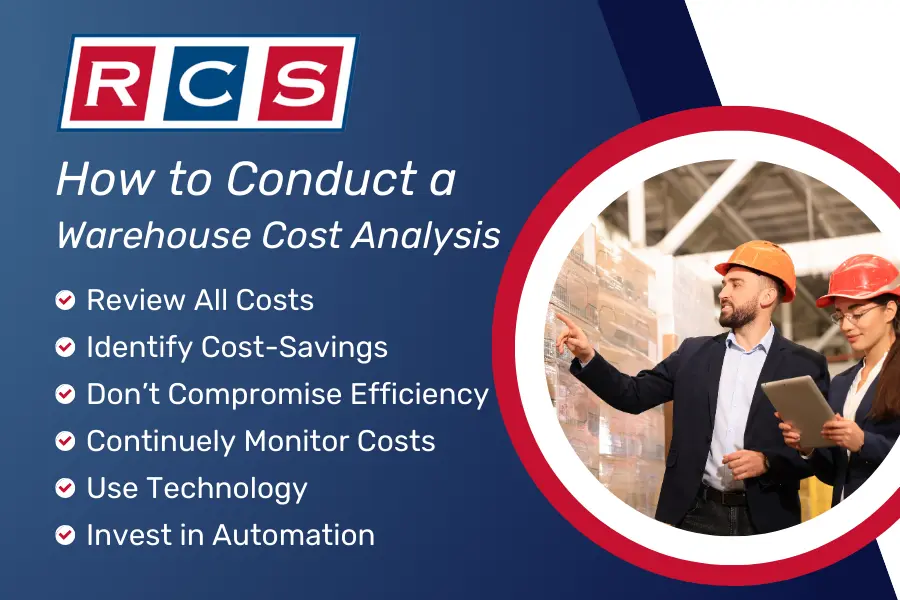
- Detailed Expense Review: Regularly reviewing all costs associated with warehouse operations is essential for a thorough understanding of financial outflows. Warehousing Express provides a complete guide to warehouse costs, emphasizing the importance of analyzing current operations.
- Identification of Cost-Saving Areas: Through careful analysis, warehouses can pinpoint potential areas to reduce expenses without impacting operational efficiency.
- Efficiency vs. Cost Balance: Achieving a balance where cost savings do not compromise the effectiveness and efficiency of warehouse operations is key. McKinsey explores different approaches to managing warehousing costs effectively.
- Continuous Financial Health Monitoring: Ongoing cost analysis is a proactive approach to maintaining the financial health of a warehouse, allowing for timely strategic adjustments. Learn Transformation offers insights into understanding and managing warehouse costs.
- Implementing Technology for Cost Tracking: Utilizing advanced software and technology for tracking and analyzing costs can provide real-time insights and aid in more accurate financial planning.
- Strategic Investment in Automation: Investing in automation can lead to long-term cost savings by enhancing efficiency and reducing labor costs, while also improving accuracy in operations.
Calculating Storage Costs: A Step-by-Step Guide
Accurately calculating storage costs is an essential skill in effective warehouse management. This process requires not just basic measurements but a deep understanding of various cost factors that impact your overall expenses. By following these precise steps, you can gain a clear and comprehensive picture of your warehouse storage costs, enabling you to make informed financial decisions and optimize your storage strategies.
{GRAPHIC}
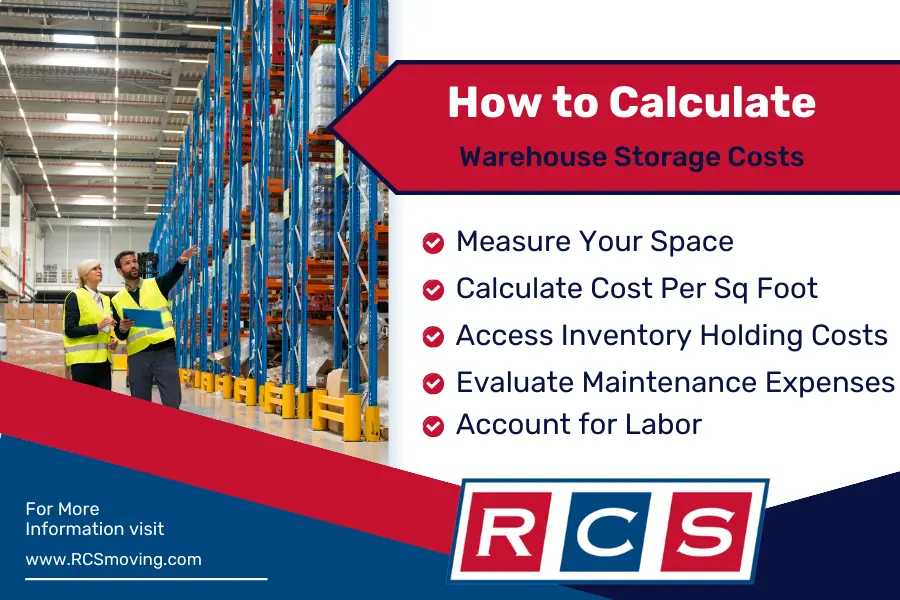
- Measure Your Space: Start by measuring the total square footage of your warehouse. This measurement is the foundation for calculating many of your storage costs.
- Calculate Cost Per Square Foot: Determine the cost per square foot by dividing your total operating costs by the warehouse's total square footage. This figure gives you a baseline for understanding the cost of occupying the space.
- Assess Inventory Holding Costs: Consider the costs associated with holding inventory, such as storage, employee wages, inventory depreciation, and opportunity costs. These costs are crucial for understanding the true cost of storing each item.
- Evaluate Utility and Maintenance Expenses: Include expenses for utilities like electricity and water, as well as maintenance costs in your calculations. These ongoing costs directly impact your overall storage expenses.
- Account for Labor Costs: Labor costs, including wages, benefits, safety, and training for warehouse staff, should be factored into your storage cost calculations as they form a significant part of operational expenses.
Enhancing Warehouse Efficiency: Key Strategies
Maximizing warehouse efficiency involves the strategic use of every available resource to its fullest potential. Enhancing your warehouse's capacity utilization rate is not just about packing in as much as possible, but about optimizing the use of space and resources in a manner that promotes safety, efficiency, and cost-effectiveness.
Here are some crucial strategies to boost your warehouse's efficiency:
- Implement Lean Inventory Practices: Adopt lean inventory methods to minimize waste and ensure that you're storing only what's necessary. This approach reduces excess stock and optimizes space.
- Integrate Advanced Technology: Utilize technology such as warehouse management systems (WMS) and automation to streamline processes, reduce errors, and increase the speed of operations.
- Optimize Layout and Flow: Reassess and reorganize your warehouse layout to ensure a smooth flow of goods and personnel, reducing bottlenecks and enhancing overall efficiency.
- Regularly Review and Adapt Processes: Continuously evaluate your warehouse processes for improvements and adapt to changes in demand, technology, and industry practices.
- Focus on Employee Training and Engagement: Invest in employee training and engagement to ensure that your team is skilled, motivated, and efficient, which is crucial for overall warehouse productivity.
- Monitor and Manage Energy Use: Implement energy-efficient practices and monitor energy use to reduce costs and contribute to a more sustainable operation.
Choosing RCS Moving and Storage for Your Relocation Needs
When it comes to commercial relocation, choosing the right moving and storage partner is crucial for a seamless, efficient transition. At RCS Moving and Storage, we specialize in providing top-notch commercial moving services that cater to the unique demands of your business. Here's why partnering with us for your commercial relocation needs is the right choice:
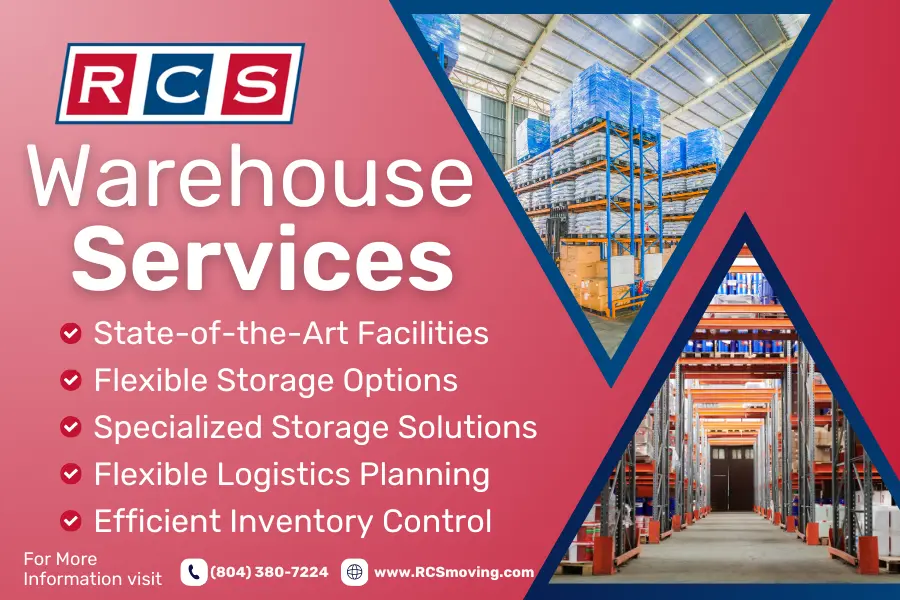
- Tailored Moving Solutions: We understand that every business has unique requirements. Our team works closely with you to create a customized moving plan that aligns perfectly with your specific needs and schedule.
- Experienced and Professional Team: Our team of professionals is trained and experienced in handling all aspects of commercial moving. From delicate equipment to large-scale furniture, we ensure every item is moved safely and efficiently.
- Comprehensive Service Range: We offer a wide range of services, including office relocations, logistics, installation services, and more, making us a one-stop solution for all your commercial moving needs.
- Efficient Storage Options: Our state-of-the-art storage facilities are equipped to handle your inventory, equipment, or any other items that need safekeeping during the transition. We offer flexible storage options tailored to your timeframe and space requirements.
- Minimal Business Disruption: We prioritize minimizing downtime during your move. Our efficient planning and execution ensure that your business operations are impacted as little as possible.
- Dedicated Customer Support: Our team is committed to providing exceptional customer service. We’re here to address any concerns and ensure a smooth and stress-free moving experience for your business.
Choosing RCS Moving and Storage means entrusting your commercial relocation to a team that values your business as much as you do. We’re dedicated to delivering a moving experience that is efficient, reliable, and tailored to meet the high standards of your commercial enterprise. Let us handle the complexities of your move, so you can focus on what you do best – running your business.
FAQ Section
Q1. How do you calculate the storage cost of inventory?
A1. The storage cost of inventory is calculated by adding all warehouse operating expenses and dividing them by the total inventory value to get a cost ratio.
Q2. What are the different types of racking in a warehouse?
A2. Different types of racking include selective, drive-in, push-back, pallet flow, and cantilever, each designed for specific storage needs and space optimization.
Q3. How do you calculate storage area in a warehouse?
A3. To calculate the storage area, subtract the non-storage space from the total warehouse area and consider the height for calculating cubic storage capacity.